I. Overview
Post-press surface treatment is becoming more and more important in packaging production. The success or failure of the current market competition depends largely on the packaging of the goods, and the quality of the surface treatment of the goods after printing determines the quality of the packaging. Therefore, we can say that post-press surface treatment is an important technical means to improve the packaging grade and strengthen the competitiveness of the commodity market.
Commonly used post-press surface treatment technologies are:
1. The surface is waxed. Mainly to make the packaging can withstand a certain amount of moisture and moisture, it was used to pack fresh meat and agricultural and sideline products in the past. This is done on the curtain flow coater by its wax coating process.
2. Laminating. Laminating film is to cover the surface of the printed product with acrylic film after printing on the packaging product, and then use adhesive to heat and press it to bond together to form a paper and plastic printed product.
The coating film can be divided into a coating film and a pre-coating film. That is, the coating film is coated with adhesive during operation, and then hot pressed to obtain a finished product. The pre-coating film is to pre-coat the adhesive on the plastic film, dry and wind it, and it only needs to be hot pressed when covering the surface of the printed product. They are completed on ready-to-coated straw and pre-coated straw.
3. Glazing. Glazing is to coat (or spray, print) a colorless transparent coating on the surface of Baolu printing, to form a thin and uniform transparent bright layer on the surface of the printed product after leveling, drying and calendering. It is completed by a glazing machine and a calender.
4. Calender. Calendering is a finishing process after glazing the printed products, and some directly calender high-grade paper products. The calendering of the printed matter is because the gloss of the glazing material after natural leveling and drying is not too ideal, and some fine printed matter must be calendered. The equipment used is a calender, and many calenders are used in conjunction with glazing machines.
5. Other special processing techniques. In recent years, there have been many post-press special processing technologies for printed products, which have developed rapidly and are popular. Common ones include surface coating (also called spraying), surface frosting (also known as sanding, that is, evenly grinding the hemp points on the surface of the printed product), embossing, embossing, embossing (concave) or simply pressing. All these new post-press finishing technologies have been seen more often in high-end packaging for daily use. It is especially common on exquisite crafts and cigarette packaging.
2. Technology development and demand
1. Packaging post-print surface treatment technology has become the meeting point of multiple disciplines and technologies
The post-printing technology of packaging has shifted from the traditional wax coating or laminating in the past to the cross technology combining the surface shape and mechanical characteristics of the printed matter. The traditional wax coating does not change the shape of the printed matter (before the surface modification), only the wax juice is attached to the surface of the printed matter after being coated.
2. New materials are constantly being applied to surface finishing
With the improvement of people's requirements for printing quality and decorative performance, many new materials have been applied to the surface finishing process of printed products. The new materials that are widely used in the finishing of printed products are mainly monologue inks and coatings of various properties. The rapid development of printing science and technology has caused printing to completely change the traditional concept of replication. Modern printing is a combination of technology and art. While it is based on the information process of high-tech foundation, more high-tech means are used to make print With beautification effect. The material basis of this beautification effect is the special performance ink and less material. For example, light-curing coatings have been used for surface finishing of printed products instead of traditional wax coating and laminating. As another example, imitation gold, silver imitation inks and coatings have been used to replace bronzing. In particular, some high-end tobacco and alcohol, high-end cosmetics and high-end gift apparel emphasize the beautiful packaging effect, which is difficult for some traditional decorative inks and coatings to meet the requirements, and has more demanding requirements for new decorative inks and coatings. It requires high production efficiency, good printing adaptability, fast drying speed, high gloss, high hiding power, good adhesion, durable wear resistance, safe use, no plugging (holes), easy cleaning, No pollution and other properties. In response to these performances and requirements, UV-curable imitation essential inks have recently been introduced at home and abroad, and are widely used in high-end cigarettes, gifts, greeting cards, invitations, calendars, business cards, advertisements, art paintings and other high-end packaging boxes (bags). For a long time to come, new special inks and coatings will remain the focus of research on surface finishing materials.
3. Post-press finishing technology and equipment update speed up
The post-print surface finishing technology has developed rapidly. In the past, the surface wax coating has already been surfaced, and the surface coating has been partially replaced by surface glazing (glazing liquid) not long ago. In the past, the general glaze drying was heated by a far infrared heater (or ordinary heater), which has the disadvantages of slow speed and easy deformation of the product. Recently UV curing coatings and inks have been rapidly promoted and applied, and there is a tendency to gradually replace coatings and infrared thermal curing coatings.
At present, the varieties and specifications of China's packaging and printing surface finishing machinery and equipment have shown a diversified pattern, and the number has reached more than one hundred. In the past, some major models and models were imported. After years of digestion and absorption, most models have been designed and produced by themselves. With the application and promotion of high technology, some old-fashioned equipment and processes have been gradually eliminated. For example, surface wax coating equipment and processes are gradually replaced by coating or glazing processes. Therefore, curtain flow wax coating machines are basically in Stalled, few manufacturers reproduce.
With the diversification of printed products, especially the consumption of various exquisite small gifts for small crafts masters, some small printing equipment and accessories have a broad market, and a new type of application field has been formed. For example, the multi-functional glue (spray glue) machine has become a popular commodity in the current market. The functions of this laminating machine include: speed adjustment, humidity and pressure control, liquid crystal display, pre-calibration function, bottom mounting equipment, general laminating and cold laminating laminating adjustments, etc. Some laminating machines can also realize color hot-printing and mounting. They can achieve ideal results in posters, inkjet printed documents, leaflets or large maps. In addition, there are other printers with origami binding, barcode label printers, etc. that have also entered the market in batches and become post-printing processing equipment.
3. Problem Analysis
1. Technical and performance issues
Compared with developed countries in the world, China still has a considerable gap in packaging and printing surface finishing technology and equipment, especially in terms of automation, viability and adaptability of related technologies and equipment. From the perspective of technology and equipment application, we are still in the initial stage. Like the technical problems of laminating equipment, domestic equipment and adhesives still have some problems to varying degrees, such as deformation problems, durability problems, separation of film and base paper, etc. There is no ideal solution. There are also coating and gluing technology and equipment for packaging and printing surfaces, which have become the mainstream of packaging surface finishing technology and equipment abroad, and our mainstream is still surface coating, all of which are yet to be resolved.
2. Device model size problem
Because many modern products rely on characteristics and personality to win the competition, and the selling cycle of a product is getting shorter and shorter, and the replacement is getting faster and faster, it is unlikely that companies engaged in packaging surface finishing will achieve a large scale. More depends on small and medium enterprises. Therefore, while improving the reliability of the equipment, the equipment model tends to be more small and medium-sized to adapt to changes in the market.
3. Energy saving problem
Printing equipment includes post-press processing equipment, the main energy consumption is its transmission and heating system, and the energy consumption occupies a greater proportion is the heating (drying) system. Most of the heating and drying are electric heating. In the past, many equipment used ordinary electric heating tubes (wire) for heating, which has high energy consumption and correspondingly high costs. Saving energy and reducing costs is the goal of the enterprise from beginning to end. At present, some equipments have adopted advanced heating and conduction methods, such as chemical thermal fluids, infrared heaters, ultraviolet heaters, etc.
4. Function and adaptability
Different materials have different properties and effects. For glazing, some use plastic substrates, some use paper substrates, and some use synthetic substrates. This does not require that their equipment can meet the glazing of these substrates and achieve the required results. In addition, for the polishing liquid, there are water-based, oily, solvent-based and so on. In addition, a new type of glazing liquid with special properties has been constantly emerging, so the finishing equipment should be able to meet the finishing requirements of these materials, which requires the equipment to have a wide range of adaptability. In addition, for enterprises that require as little equipment and space as possible, complete as many finishing operations as possible to reduce processing, storage and transportation costs. As a result, multi-functional glazing calenders, laminating glazing machines, calendering concave molding machines, glazing die-cutting machines, etc. have appeared one after another.
5. Reliability problem
Reliability is the first consideration in the design of any packaging and printing equipment. The fierce market competition requires that the equipment can be quickly adjusted to customer product requirements, replace different components and mechanisms, and can be easily operated and reliably controlled and operated to improve the accuracy and efficiency of processing.
Surface finishing technology has been applied to various non-professional fields. Such as various types of daily necessities, cultural items, decorative items, handicrafts, etc., many of the personnel used do not have professional skills, and the operation is not as handy as that of professionals. This requires mature technology and reliable equipment. Reliability is an important guarantee for the extension and penetration of packaging and finishing equipment and technology into other industries and fields.
Advantages of charcoal barbecue:
Big fans of charcoal Stainless Steel Bbq Grill will never choose a gas barbeque. They do have a point: charcoal ovens can reach a ferocious 482 degrees Celsius on the surface of meat, much hotter than standard gas ovens without infrared burners. Using this heat allows the skin of steak and lamb chops to turn into our beloved pastry, while maintaining the red and pink color inside the meat.
Another major advantage of charcoal roasting is smoke, an interesting by-product of burning. Charcoal smoke contains a wide range of flavor molecules, especially when ignited. Gaseous fuels are simple molecules (CH4 is natural gas, C3H8 is liquid propane). If they were completely burned, there would be only water and carbon dioxide, no flavor. In order for a gas oven to produce smoke, wood must be added. When the fat and juice of food drips onto the burning charcoal, a great deal of smoke is produced. If there is only a brief encounter with smoke, it does not significantly alter the flavor of fast-cooking foods such as hot dogs, beef burgers, or even lean steaks. In thick cuts of steak and chicken, the flavor produced by the smoke can be clearly perceived. There is a noticeable difference in flavor if you use your corten steel bbq for a long, low smoke roast. The flavor of the smoke produced by the gas oven is very simple.
Name | Outdoor gas grill corten steel metal barbecue |
Material | Corten steel |
Cooking plate Size | Diameter 1000mm |
Base Size | 500*500*700mm |
Thickness | Base:2mm, Cooking plate:10mm |
Weight | 120KG |
Packing | Pallet/carton/wooden box packing |
Packing
Packing will by pallet/carton/ wooden box,according to different demand.
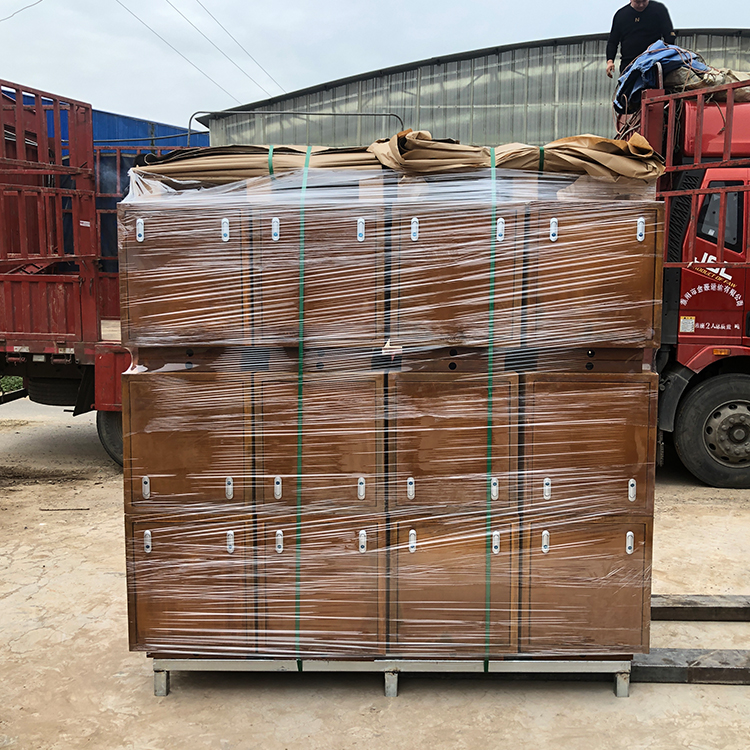
Gas Bbq Grill,Propane Grill,Gas Barbecue,Natural Gas Grill
Henan Jinbailai Industrial Co.,Ltd , https://www.hnjblbbq.com