Our company introduced the MK1060ER all-disposal die-cutting machine in early 2014. However, in the initial production process, the equipment has problems such as unstable box-splitting device and uneven product delivery, and the production speed is slow, which is 4200 sheets/hour. . To this end, our company set up a technical research team, starting from the three major positions of die cutting, stripping, and boxing, so that the full-cutting die-cutting has the greatest effect.
——Jinan Quanyong Printing
Die cutting station change
1. Selection of die cutting board
The use of sandwich steel die-cutting, combined with the use of fully enclosed frame, can achieve an ideal overall die-cutting effect. Although the cost of sandwich steel die-cutting is relatively high, its high processing precision and long service life have resulted in high quality and stability, which has never been able to match other types of die-cutting plates. Combined with the use of fully enclosed frame, it will be the best choice for a large number of orders, and is also an important condition for stable production and efficiency improvement in the die cutting process.
Of course, in the actual operation process, the installation of the sandwich steel die-cutting plate has higher requirements on the operator's skill, including the locking of the die-cutting plate, the installation of the steel bottom die, the padding of the die-cutting pressure, etc., all need to be careful. Operation, as this will determine the boot speed of the device and the quality stability of the product. Table 1 compares the use of sandwich steel die-cuts (with full-closed plate frames) with ordinary wood die-cuts.
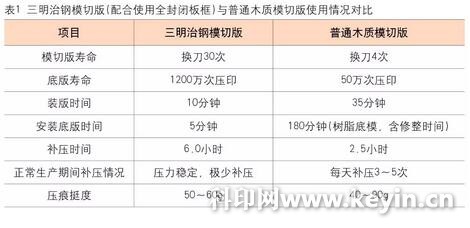
2. Design of the connection point
In the all-disposal die-cutting process, the following principles are generally followed for the planning and design of the connection point. The first is the principle of “deeply hiddenâ€, that is, first consider the position of the connection point in the fold line of the cigarette pack to avoid carton molding. The rear connection point is exposed outside, which affects the appearance of the product; the second is the principle of “strong combinationâ€, that is, a strong connection point is created on the running track of the tooth decay to ensure the die cutting speed and fully utilize the full die cutting The advantage of the machine, at the same time reduce or reduce the connection point near the edge of the cigarette packet; the third is the "peaceful reunification" principle, that is, try to connect the connection point in the same position of the single product to ensure the appearance consistency of the product after mass loading The fourth is the principle of “less is betterâ€, that is, the smaller the total number of connection points, the better.
Figure 1 is a schematic diagram of the connection point of 18 cigarette packs and small box products determined by our company's full stripping die-cutting machine after repeated tests. Wherein, the width of the axial connection point is 0.2-0.3 mm, the width of the connection point of the paper-feeding direction is 0.3-0.4 mm, and the connection point of the paper-feeding direction should be designed on the running track of the tooth-tooth to enhance the paper level. Paper stability.

3. Stability of semi-finished products
The full-clearing die-cutting machine cannot be sampled at any time, which requires better quality of the semi-finished product (upper process incoming material). Therefore, the stability of indicators such as water content, paper thickness and flatness of semi-finished products is also an important factor affecting the production efficiency of the whole blanking die-cutting machine.
Optimization of waste disposal stations
1. Selection of material and structure of stripping board
In terms of the material of the scrapped version, the resin material of the harder electronic version is used to replace the original wooden material to ensure the rigidity of the layout and improve the matching precision when working up and down the scrap version.
In terms of the waste plate structure of the supernatant, the integrated cleaning and scrapping plate is tailored for different die-cutting plates, and the conventional cleaning waste needle is replaced by a stripping knife having the same shape as the waste-removing portion. The integrated cleaning and scrapping version is easy to install, and only needs to complete the overall positioning when changing the plate. Of course, a rebound sponge with a moderate height and moderate hardness is also an indispensable auxiliary condition.
In terms of the structure of the scrap in the middle and the Qing Dynasty, in order to ensure that the scrap has “no return†during the cleaning process, we have improved the trapezoidal angle of the waste hole and improved the apex angle, and at the same time the “small plane†(the red box in Figure 1) The tip end portion of the exhaust hole corresponding to the position is shortened by 1 to 2 mm. In addition, in order to solve the problem of four "90-degree ears" (green frame in Fig. 1) die-cut connection (not open), a "bump module" with a height of 2 ~ 3 mm is installed at the corresponding position of the scrap version of the middle and the middle. By the pressure of rebounding the sponge during the stripping, the four "90-degree ears" are pressed open, thereby improving the applicability of the cigarette pack. Currently, the technology has applied for related patents.
2. The application of the waste needle
Through the above improvements, the stability of the waste disposal station has been greatly improved, and the production speed has been increased from 4,500 sheets/hour to 5,500 sheets/hour without using the waste needle. In order to further increase the production speed, we installed a small amount of waste needles at the side of the towed waste to ensure the instantaneous speed when the waste side fell.
Optimization of the binning station
The box-separating station is the fundamental part of the all-clearing die-cutting machine, which is different from the ordinary stripping die-cutting machine. It is also the core technology of the all-clearing die-cutting machine. Our company cooperated with Yuehe Xing Laser Knife (Shenzhen) Co., Ltd. to carry out a relatively thorough technical transformation of the original sub-box system.
AUTRENDS INTERNATIONAL LIMITED , https://www.petspetsdoggze.com